Thrust Bearings Of NSK
Thrust Roller Bearings of NSK include products using cylindrical rollers and products using spherical rollers. Although this type of bearing can only bear axial loads, it has the characteristics of being suitable for bearing heavy loads and high shaft rigidity. Among them, the thrust spherical roller bearing, the center of the roller bulges, has a self-aligning function, so this bearing is not affected by installation errors and shaft deflection. The standard configuration of the retainer is a machined brass product; the E-type product uses a stamped retainer, which has the characteristics of large load capacity.
Working principle of thrust bearing
For the thrust bearing, a wedge-shaped gap is formed between the thrust bearing and the pad, and the thrust disk rotates. Due to the certain viscosity of the lubricating oil, the thrust disk brings oil into this gap, the oil inlet is large, and the oil is discharged. With a small opening, an oil film pressure is formed in the oil wedge to withstand the axial thrust of the rotor.
In order to obtain liquid lubrication, the dynamic pressure bearing must meet the requirement of wedge-shaped gap in structure, so that the oil inlet is large and the oil outlet is small. The formation of the bearing oil film and the amount of oil film pressure are affected by factors such as the speed of the shaft, the viscosity of the lubricating oil, the bearing clearance and the load on the bearing. In general, the higher the speed of the shaft, the greater the viscosity of the oil, the more oil is brought in, the greater the oil film pressure, and the greater the load. However, if the viscosity of the oil is too large, it will cause uneven oil distribution, increase friction loss, and cannot maintain a good lubrication effect. If the bearing clearance is too large, it will be detrimental to the formation of oil film and increase oil consumption. If the bearing clearance is too small, the amount of oil will be insufficient, which cannot meet the requirements of shaft cooling. A certain bearing structure can only bear a considerable load at a certain speed. If the load is too large, the formation of oil film will be very difficult. When the bearing capacity of the bearing is exceeded, the bearing shell will be burned out.Click here to buy NSK Bearing 32BD4718DDukCG26.
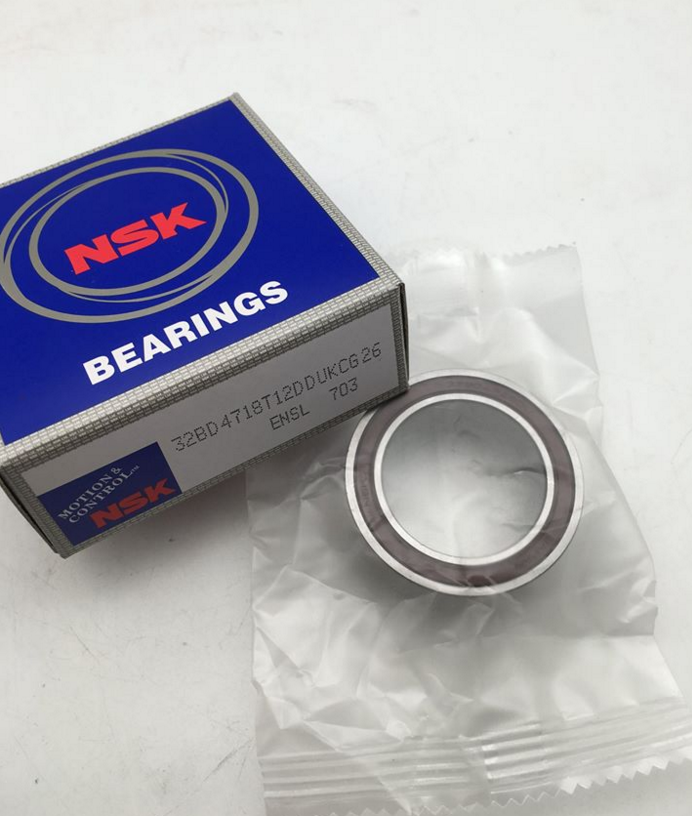
The NSK thrust bearings commonly used in centrifugal compressors are Michelle thrust bearings and Kingsbury thrust bearings. Their common feature is that there are multiple movable thrust pads, and there are bearing points behind the pads. The thrust pad can swing around the fulcrum to form the best lubricant film.
The base rings between the thrust pads of the Michel thrust bearings are in direct contact and are single-layer (as shown in the figure below). When the thrust pad is under thrust, the position of the thrust pad can be automatically adjusted to form a favorable oil wedge. Main thrust pads and auxiliary thrust pads are divided on both sides of the thrust plate. Under normal circumstances, the axial force of the rotor is transmitted to the main thrust pad through the thrust disk through the oil film, and then to the bearing seat through the base ring. However, reverse axial thrust may occur during starting or load rejection. This thrust will be borne by the secondary thrust pads. The side of the thrust pad contacting the rotor thrust disc is lined with Bajin alloy. Its thickness should be less than 1-1.5mm. And inclined to the direction of rotation of the rotor, so that through the relative movement of the rotor anti-spreading plate and the thrust pad surface, an oil wedge bearing axial thrust will be formed between them.
The advantages of Michelle thrust bearings are simple structure and small axial size; the disadvantage is that when the thickness of the pads is slightly different or the parallelism between the bearing base ring and the thrust discs is error, the load between each pad cannot be adjusted, Some tiles are overloaded.Need NSK Bearing 24038CAME4 03 S11,click here for more details.
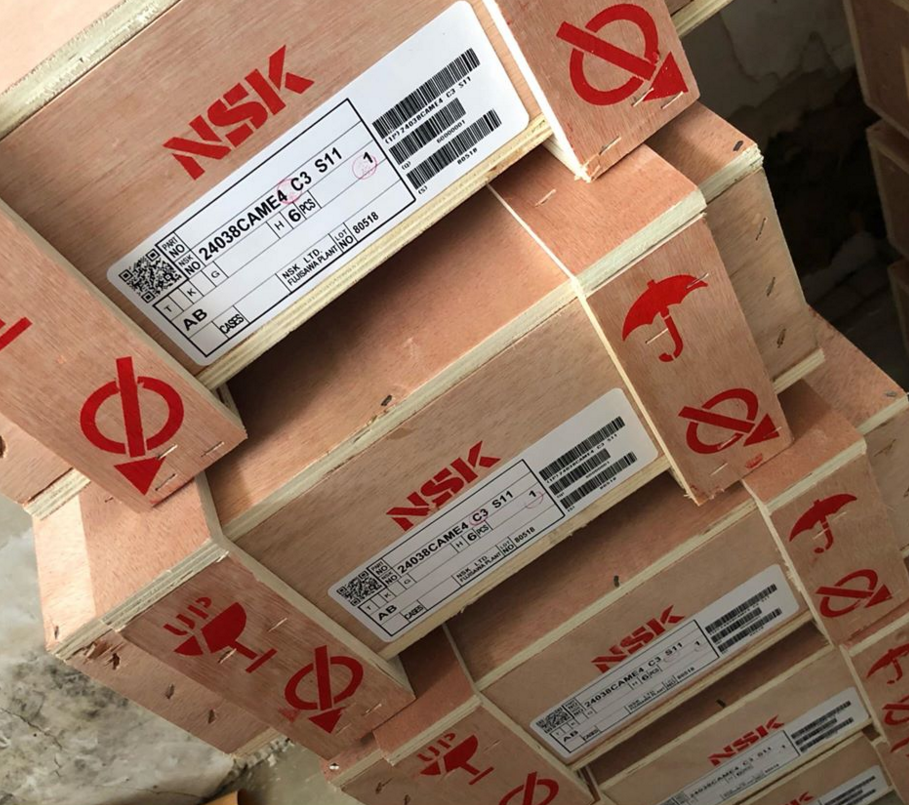
There is an upper level block and a lower level block under the thrust pad of the Kingsbury thrust bearing. Then it is the base ring, which belongs to the three-layer structure (as shown in the figure below). Thrust pad and upper level block, lower level block and base ring underneath. Spherical fulcrum contact is used between them to ensure that the thrust pads and level blocks can swing freely, so that the load distribution is even. Thrust tiles generally use 25 copper. Casting babbitt alloy above, the thickness of the alloy is generally 1-1.5mm. There is a gap between the thrust plate and the thrust pad. This gap is usually called the total working channel, which is generally 0.25-0.40mm, which can ensure that an oil wedge is formed between the thrust plate and the pad to bear the rotor’s Axial thrust. Lubricating oil enters the gap between the thrust disk and the thrust pad from the gap between the bearing seat and the housing. The oil discharge is due to the centrifugal force when the thrust disk rotates. The oil is thrown out and discharged from above the bearing seat.
The advantage of the Kingsbury thrust bearing is that the load distribution between the pads is uniform, the adjustment is flexible, and the rotor misalignment and deflection can be automatically compensated. The disadvantage is that the structure is complicated and the axial installation size is long.
The requirements of centrifugal compressors for bearings are safe and reliable, stable operation, good vibration resistance and long service life. In order to better meet these requirements, radial bearings and thrust bearings are constantly being developed and improved. At present, the newly designed and manufactured centrifugal compressors have adopted tilting pad radial bearings and Kingsbury thrust bearings. Moreover, structural improvements have been made to the tilting pad radial bearing and the Kingsbury thrust bearing, which greatly improves the reliability and stability.